Originally submitted at Hardware Sales Inc.
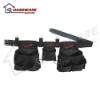
Milwaukee's Heavy-Duty 33 Pocket/3 Piece Tool Belt is made from water-resistant 600 Denier Ripstop Polyester Material. The Tool Belt features 33 total pockets of various sizes and shapes, large flat bottom pouches, builder's square pockets in each large pouch and a cell phone or 2-way radio...
Milwaukee 49-17-0190 Heavy-Duty 33 Pocket/3 Piece Tool Belt
The perfect tool belt for me
By CarpentryGuy from Nashville, TN on 2/27/2010Pros: Holding Capacity, Comfortable Fit, Versatile, Durable
Best Uses: Multi-Purpose
Describe Yourself: Professional
I'm a contractor and I handle a wide range of projects from framing to tilework. I wanted a tool belt that had some pouches, but also had lots of pockets to organize my tools. My last tool belt had just a couple big compartments and my tools were always getting lost in the bottom.
I was pleased when I got the Millwaukee belt because of the number of pockets and how they were organized. I also love the two 'bottomless' pockets which will hold my small flatbar and my drywall saw. It's also easy to remove one of the pouches from the belt if you don't need all of your tools for a particular project and want a lighter load.
I'm completely happy with this tool belt, and the price made it a no-brainer.
(legalese)